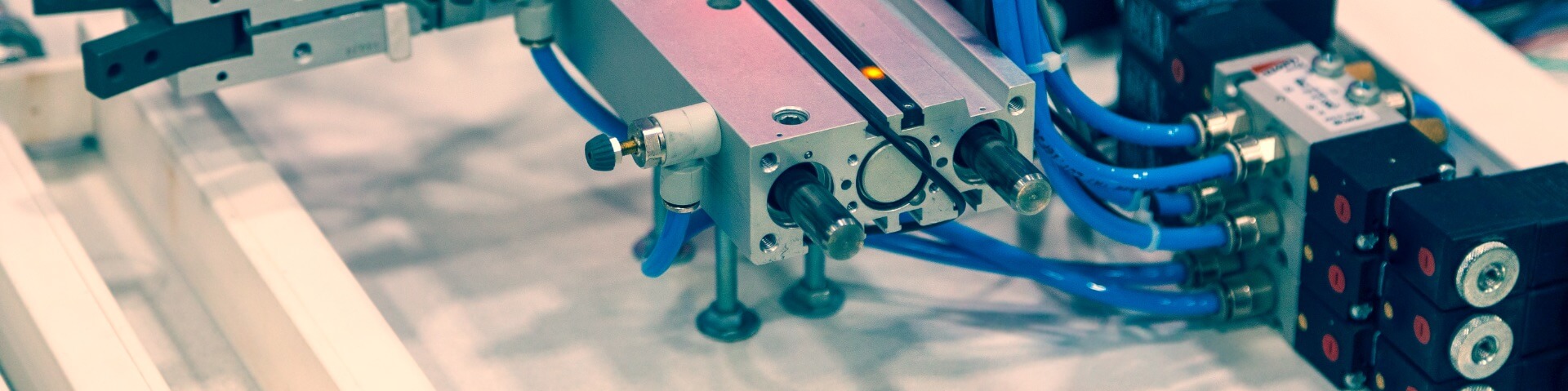
3D Printing FAQs
Rapid PSI takes the time to provide you with answers to some of your pressing questions involving additive manufacturing and 3D printing.
Equipment/Material Questions
What applications fit Selective Laser Sintering (SLS) well?
The following can fit for SLS 3d printing:
-
-
-
- Parts that need good detail and strength
- Fast and cost effective on small parts
- Fast lead times
- Thin walls are printed well
- Ability to pack parts for cost reduction
-
-
What type of projects typically fit stereolithography (SLA)?
- Good detail/surface finish
- Array of materials including clear.
- Best option for master patterns for cast urethane.
How big of a part can you print?
Our largest machine can print 36” X 24” X 36”. If a part is larger than that envelope, we have software that cuts the CAD model into sections to print within that envelope. We then bond the parts together.
How many 3D Printers does Rapid PSI have in-house?
We have 24 total printers to service our customers.
How many F900s does Rapid utilize?
We run 4 F900s and another 4 900mc machines.
What is the hardest material to run?
Ultem 9085 is by far the trickiest material we run. It likes to move and shrink more than other materials. However, it is FST rated, passes burn tests, and can be used in interior aircraft cabins which makes it a valuable printing material.
What material would you recommend for tooling applications?
For overall strength and stability, we generally run tooling out of PC or Ultem 1010. Ultem 1010 also has the ability to grow in .020 layer thickness which speeds up runtime significantly which reduces project costs.
Quoting and Process Questions
Can you quote/build from 2d drawing?
No. To even get a quote, we need a CAD 3D model to quote from. There is no way to build a part without a CAD model.
Where do I send files to get a quote?
You can upload files on our website by clicking on the Get Quote button at the top of each page. You will be required to fill out some information before submitting your files so we know who to send the quote to.
Does Rapid PSI accept ITAR projects?
Yes, Rapid PSI is ITAR compliant.
Does Rapid PSI do post processing?
Yes, including installing inserts, bushings, and assemblies.
What is Rapid PSI’s competitive advantage?
We have significant FDM capacity: (14) 400mc printers / (8) F900-900mc printers / (1) 450mc
Does Rapid PSI print metal parts?
Rapid PSI does not have metal printers in house. We use our trusted partners who have years of experience in metal printing to build those parts for us and our customers.
Do you do work overflow for other companies that have printers themselves?
Yes, most of our customers have their own machines. They utilize Rapid PSI overflow work or when timing is critical, or they do not have enough machines in house to meet a deadline. Sometimes a customer doesn’t have a material option on their machine, so they will outsource to Rapid PSI.
How to you print parts so quick and meet deadlines others cannot?
The reason we can usually get parts out quick is because we have the inventory of material in stock and many printers. Sometimes the lag with other companies is because they must order in material to get a job done.
What do you need to quote a part?
We need a CAD file to provide pricing. We do not provide pricing off pictures, 2D drawings, or prints.
Can Rapid PSI build parts to a customers Process Control Doc or Specification?
Yes. Rapid PSI builds to many different customer specifications. We can do whatever is required of a customer specification. Ex. Dewpoint test/monitoring, temp test/monitoring, doc control, file control, tensile bars, calibrations.
How much will a part cost?
We need a model to price out a build. Orientation of a geometry greatly affects the price of a part.
What is a normal lead time?
Lead times can be as little as one day and as long as 2 weeks. It is heavily dependent on the size of the part and quantity.
Quality Questions
Does Rapid PSI do First Article Inspection Reports?
Yes. We price the process of inspection into the builds when requested.
Can material certifications be provided with my parts?
Yes, every material we 3D print can have material certifications backing them up.
What kind of testing do you perform?
Rapid PSI can provide Burn Testing, Tensile Testing, and Load Testing.
How do you ensure your FDM machines are running correctly?
We have a quality system in place to ensure maintenance and checks of our systems. Rapid PSI does temperature calibrations on the machines every three months, and we calibrate the extrusion heads to ensure uniformity across all systems here.
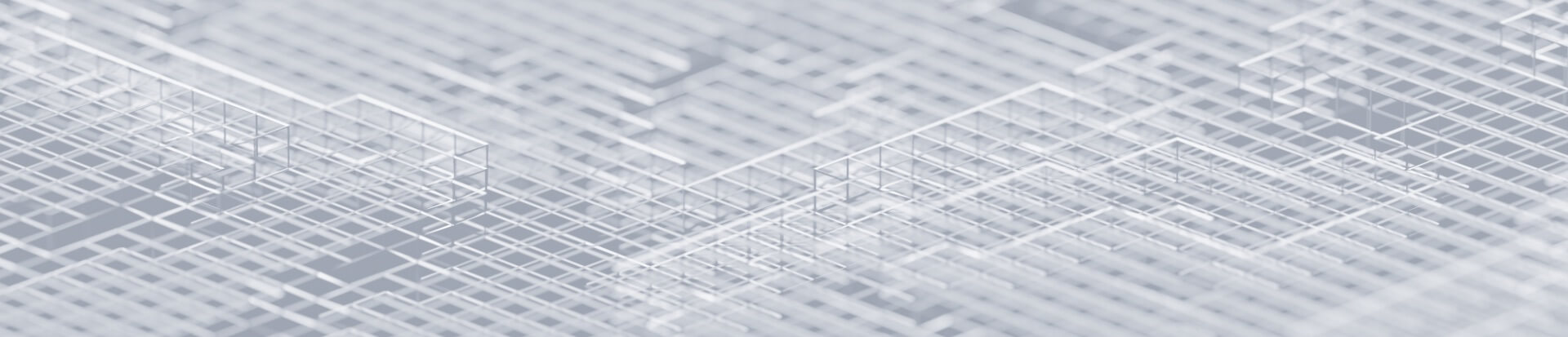
Are you interested in learning more? Take a look at our service pages listed below, fill out a contact form to reach us, or call (316) 265-2001 today!
- 3D Printing and Additive Manufacturing
- High-Volume Production
- Rapid Tooling
- Rapid Prototyping
- Aerospace Manufacturing